Experts in carbon emissions associated with buildings contend the Government’s target to build about 33,000 new homes every year until 2030 will compromise Ireland’s ambitious emissions reduction targets unless low-carbon approaches to building can be embraced across the building sector.
Building more timber-framed homes using Irish timber seems like an obvious place to start yet current building regulations in Ireland prevent the use of timber frames in buildings more than 10 metres (three storeys) high.
Forestry Industries Ireland (FII) and other groups are currently lobbying for change to this height limit for timber-framed buildings. This would require amendments to Part B of the building regulations, which focus on the fire safety measures in building design.
“There is currently a conflict between the Government commitment to decarbonise the built environment, and the housing and fire safety policies,” Des O’Toole says, a structural engineer with Coillte who is on secondment to FII.
The group has looked at other European countries where timber-framed buildings are allowed up to 80 metres (24 storeys) in height and in the UK where timber-framed buildings are permitted up to 18 metres if there are sprinkler systems in place.
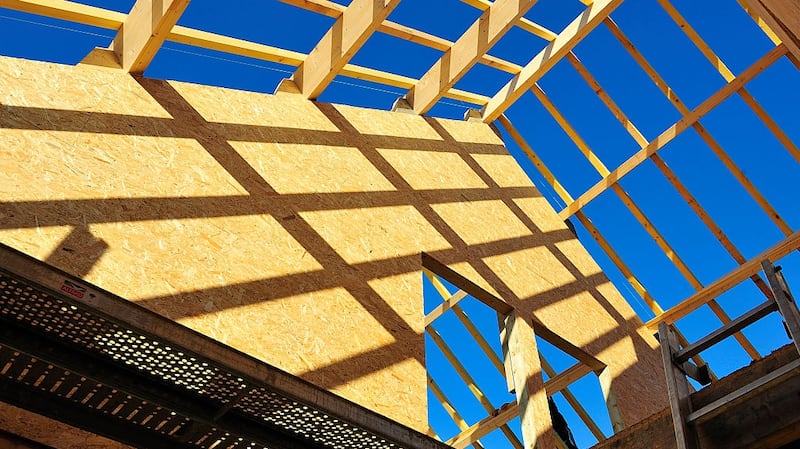
“We’ve suggested that a new cross party joint Oireachtas group could look at the issue in the context of low-carbon building materials and regulatory changes,” O’Toole says.
Currently in Ireland, large scale housing developers such as Cairn Homes and Glenveagh Homes are using timber frames in more and more of their housing developments but smaller building contractors remain committed to masonry built homes.
“About 48 per cent of all new scheme homes are timber-framed now yet timber frames cannot be used in medium rise construction (four storeys and above) where there will be growing demand in higher density developments up to 2030,” O’Toole adds.
Joseph Little is head of building performance and construction at the School of Architecture, Building and Environment at the Technological University of Dublin (TU Dublin). He says that aside from specific restrictions in the building regulations, there is a cultural bias towards masonry, steel and concrete in this country both among builders and from training bodies.
“Most engineering schools aren’t doing enough to embrace timber and very few undergraduate engineering programmes provide even one module focused on timber in four years of education. There is a tendency to treat timber like a weak steel instead of a material with complex but really exciting properties,” he says.
The Timber Engineering Research Group at the University of Galway is the exception. It supports the use of timber as a sustainable construction material by performing technical and scientific research to create a broader understanding of timber and engineering wood products.
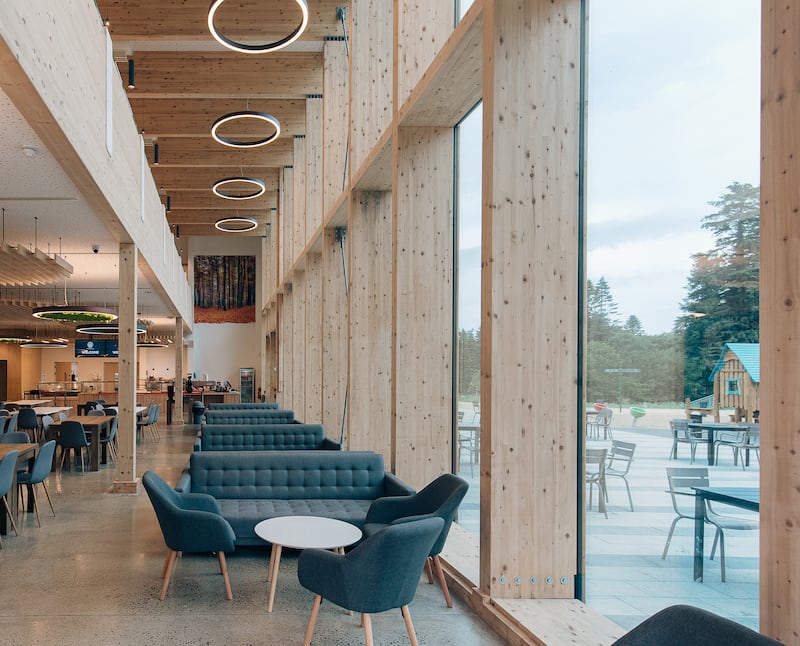
Current research projects co-ordinated by the University of Galway include SAOLWood, a study into the life cycle assessment of Irish timber use in the built environment. “By quantifying the environmental, economic and social impacts of locally sourced Irish timber products, this research should support informed decisions by building designers, contractors, planners, developers and policymakers,” Dr Patrick McGetrick says, principal investigator and lecturer in civil engineering at the University of Galway.
Another study (MODCONS) explores the use of Irish timber in cross-laminated panels for walls and floors in terms of its structural integrity, fire, acoustic and vibrational impact, and the possibilities for reuse following deconstruction. A paper from the MODCONs project team published in April demonstrated that Cross Laminated Timber manufactured from Irish-grown timber performs well under fire loading and complies with European Structural Design Standards.
“This latest study – in which we partnered with Munster Technological University – showed that Irish timber can be safely used for buildings,” Dr Conan O’Ceallaigh explains, research fellow and lecturer at the School of Engineering at University of Galway.
Most developers (in Ireland) use timber from Scandinavia because it has a [slightly] higher strength classification and is less knotty in appearance than Irish timber
— Joseph Little, head of building performance and construction at the School of Architecture, Building and Environment at TU Dublin
A spokeswoman for the Irish Green Building Council (IGBC) says timber construction is typically less human and resource intensive, and faster to build. “This is because most of it is built off site. Transitioning to more timber buildings could contribute to a reduction of our carbon footprint while supporting the faster delivery of affordable homes at scale,” Marion Jammet from the IGBC says.
According to the IGBC, Environmental Product Declarations (EPDs) show that bio-based materials including timber generally have lower embodied carbon compared to steel and concrete. The EPD Ireland programme, which was created by the IGBC, allows manufacturers of construction products to provide third party verified transparent information on the environmental impacts of their products.
Architect and engineer Prof Michael Ramage, who is the director of the Centre for Natural Material Innovation at the University of Cambridge, has said 80 to 90 per cent of buildings of 15 storeys or less could be constructed from timber. In his Tedx Cambridge University talk, Ramage says he expects to see our skylines dotted with skyscrapers of wood in the next decade.
“The goal is to replace steel and reinforced concrete towers with a more sustainable alternative. Engineered timber materials like cross laminated timber are bigger and stronger than trees. We need to move to a building tradition where what we build is grown and not mined,” he says.
There is no technical reason why we can’t build timber-framed houses with 100 per cent Irish timber
— Des O’Toole, a structural engineer with Coillte
Lighter timber-framed structures also permit the addition of upper floors to renovated buildings in cities where the underground rail networks prevent heavier concrete floors from being added. Experts say that since wood is four times lighter than concrete, lower concrete buildings can be replaced with taller timber framed buildings.
However, one ongoing issue in Ireland is that even when builders opt for timber frames rather than bricks, cement and steel, the timber used is usually imported from Scandinavian countries.
“Most developers use timber from Scandinavia because it has a [slightly] higher strength classification and is less knotty in appearance than Irish timber. Yet 80 per cent of Irish timber is exported to other countries (mainly England) where much of it is used in timber framed buildings,” Little explains.
However, one Irish company, Dempsey Engineering is leading the field and using Irish timber for timber framed homes. It’s no coincidence that Dempsey Engineering is owned by the Glennon Brothers, who are the largest players in the saw mills business in Ireland. Now as part of their efforts to promote the use of Irish timber in Irish house building, Coillte is working with the Glennon Brothers to construct a demonstration home in the summer of 2023 in which all timber used will be 100 per cent sawn timber and panel products.
O’Toole is also hopeful that new forestry targets, which will ramp up timber production in Ireland, will result in more Irish timber being used here going forwards.
“There is currently about 3.5 million cubic metres of logs harvested every year in Ireland and more than half of this goes to saw and board mills and on into construction in Ireland. Timber production is set to double to about seven million cubic metres over the next 10-12 years and it will be the priority of saw and board milling sector to increase their markets and create new markets,” he says.
“There is no technical reason why we can’t build timber-framed houses with 100 per cent Irish timber – especially in the higher density housing that is being built now,” O’Toole says.
The recently updated Woodspec guide to the use of Irish timber in buildings should help engineers, architects and builders develop a better awareness of the myriad use of this low-carbon material in future housing.