An €8.2 million project to pioneer production of anti-reflective, scratch- and abrasion-resistant surfaces, will be led by researchers based at Trinity College Dublin after Dr Parvaneh Mokarian was appointed as the project's "key co-ordinator".
The four-year Sun-Pilot project is hoping to develop solutions for the optics and automotive industries, however Dr Mokarian outlined how the product can also be used for more commonplace consumer items such as mobile phones.
Its potential appears to be significant and its application wide-ranging with unlikely parties declaring their interest in the project. One manufacturer of interior car parts said the technology could allow them to cut down on the use of metallic interiors. They suggested that plastics will have to replace metallic materials because of the latter’s high levels of Co2 emissions.
However, plastics don’t have the same feel, so the sun-pilot material could allow them to have the same functionality and feel as metallic materials. They believe that by manipulating light, you can change the feel of surfaces.
That manipulation of light is key to the function of the innovation. By creating multilayer coating with a single nano-patterned surface, Dr Mokarian estimates her team can manufacture the technology for 75 per cent less than the current thin-film coating offerings.
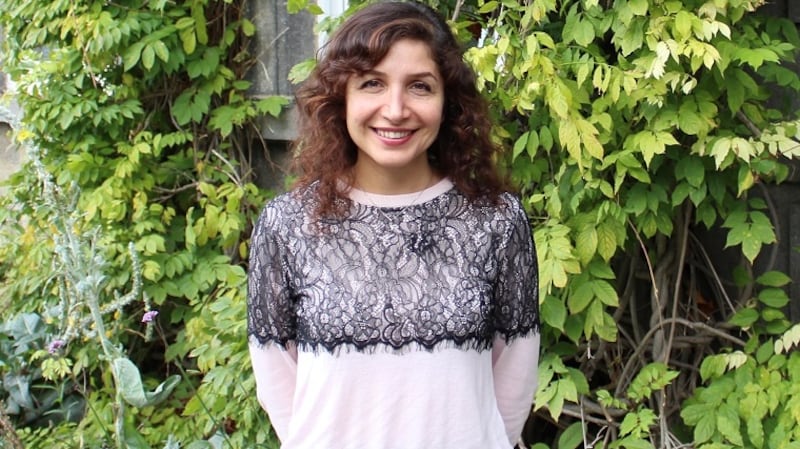
“Current anti-reflection solutions typically rely on thin-film coatings comprising multiple layers of materials deposited on to each and every reflecting surface along the optical path. These coatings require careful design and engineering of the thicknesses and refractive index of the thin-films, and batch processes that involve relatively high temperatures. This is not commercially viable with plastic screens used, for example, in tablet and mobile phone screens,” she said.
The way the technology works is that it manipulates light by creating nanostructures that can be put on an item’s surface. The surfaces will also provide superior wear-resistant properties compared with coated solutions and will offer new self-cleaning and anti-microbial properties.
“This technology has been inspired by nature,” Dr Mokarian explained. “If an insect’s eye reflects light, when they look at their prey they will see the reflection and escape. So, nature made the structure in the insect’s eyes so their prey wouldn’t see the reflection. We’re trying to bio-mimic that,” she added.
Aside from car interiors and the optics industry, consumers could find it on their mobile phone screens in the not too distant future. The nanostructures could ultimately suppress the light reflection from the surface so, on a sunny day, people would still be able to see their screens.
Scaled up
Of course, all of these uses are some time off. The project won’t end until December 2021 and at that point, the researchers expect it to be in “proof of concept” phase. After that it will need to be scaled up so that it can be used for manufacturing purposes.
That also requires it to be relatively cost-effective. “If the money doesn’t make sense, nobody will go for it,” Dr Mokarian said. But for certain industries it could make more financial sense than others.
For the solar industry, as an example, the technology would be perfect for solar cells because it captures every photon of light, according to Dr Mokarian. While it would improve efficiency for that industry, it would have to be relatively cheap because people are only willing to pay so much for electricity.
In the biomedical sector, however, price isn’t as much of an issue with individuals and health providers willing to pay for technologies that make the provision of health more comfortable and safer for patients. With this technology you can reduce the size of cameras being sent into a patient’s body without reducing the level of light. The result is a considerably less invasive surgery for patients without compromising on quality.
While some estimates put the global market for anti-reflection coatings at more than $6.1 billion (€5.17bn) per year by 2021, they have yet to take off because of the high cost of the current technology and the lack of durability in challenging environments.
The advantage of Dr Mokarian’s “Zeroptica” technology is that, as it is solution based, it can be applied to curved surfaces and large areas. Additionally, it doesn’t require expensive equipment or harsh chemicals – both of which can be costly.
While Dr Mokarian and her team have achieved significant funding from both the European Horizon 2020 scheme as well as industry. She recently won an award at the Trinity Innovation Awards.
Dr Mokarian is a senior research fellow at materials centre Amber, which is funded by the Science Foundation Ireland. Including Amber, the project involves 13 partners from six European countries included five multinational companies, four small and medium enterprises, two universities and two research institutes.