Heavy industries using intense heat in their manufacturing face the hardest task in trying to decarbonise and wean off large amounts of fossil fuels.
Irish Cement has been on that journey for some years but now plans to scale up efforts at their cement-making facilities by changing the fuel mix used in their kilns at Platin, Co Meath, and Mungret on the outskirts of Limerick City.
Bord Pleanála granted permission in April for a change of fuel use at both locations, which was opposed by environmental groups – in the latter case, there were over 1,400 objections. The EPA is due to adjudicate on licensing the new arrangements in coming months.
Cement manufacturing is a highly competitive business and the proposed developments were essential to ensure the long-term viability of both plants, Irish Cement pointed out repeatedly. Mungret is one of the last cement factories in Europe totally dependent on fossil fuels.
Replacing fossil fuels with recyclables in cement factories is standard practice throughout Europe, and is line with EU, national and regional waste management policy, explains Brian Gilmore of Irish Cement in the course of a visit to its Platin facility.
In particular, it fulfils the requirements of "a circular economy" in which materials are brought back into the system at the end of their life rather than discarded, in pursuit of a low-carbon, sustainable society, adds Gilmore he is marketing and communications manager with the CRH subsidiary.
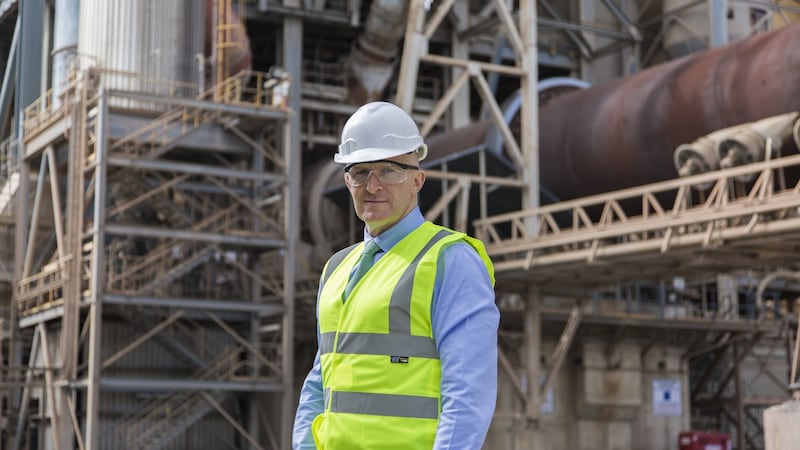
The European Commission last year flagged this form of "waste to energy" a form of co-incineration of waste in a combustion plant – is a distinct and acceptable element of the waste hierarchy. Initially, it was considered a valid way to end over reliance on landfill but Gilmore points to a range of environmental benefits in Irish Cement's case while also helping to increase the competitiveness of their operations.
Being allowed pursue this route which is a change of fuel, not change of use, he underlines “will reduce Platin’s dependence on imported fossil fuels, reduce carbon dioxide emissions by up to 300,000 tonnes per year, and help recover valuable resources that might otherwise end up in landfill by providing a reliable outlet for ‘non-recyclable’ residual waste.”
The latest permission allows 600,000 tonnes of alternative fuels a year to be used. Initially, this will be in the form of Solid Recovered Fuel (SRF), a residual waste after recyclables have been removed, though other materials are permitted such as old tyres and meat and bonemeal, but there are no plans to use them in Platin at the moment.
[We are] making a product, the second most used material on the planet after water
It’s a clean dry blend of fragments of plastics, paper, cardboard and textiles which arise once recycling of waste materials through mechanical and biological treatment has been completed. A lot of it comes from green bins.
There is no recycling option in Ireland for plastic film, he notes, but "it's perfect for use in the cement industry" – similarly, bags with foil layers, composite packaging and non recyclable single-use coffee cups.
Previously, it had permission to use 120,000 tonnes per annum of alternative fuels. This improved competitiveness, especially in securing overseas customers (40 per cent of its cement is exported), but by 2016 it hit capacity limit and fossil fuels filled the gap. “This is despite the fact that suitable SRF is available from existing suppliers, who continue to invest in additional SRF production facilities and production capacity.”
Making cement
“You cannot make cement without the intense heat inside the cement kiln, which is required to, literally, melt the raw materials,” he says.
Crushed limestone rock (delivered from Platin’s adjoining quarry) is combined with smaller quantities of ingredients including silica, alumina and iron and then ground, mixed and fed into the large “K3 kiln”.
A temperature of 1,450 degrees plus inside the kiln is needed to produce good quality clinker. The clinker is subsequently ground on site to produce cement used by the construction industry.
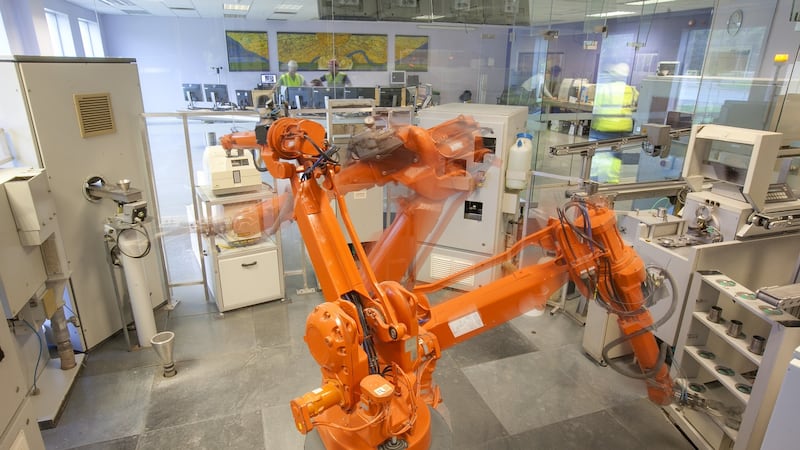
Complete combustion occurs inside the kiln so no residual wastes are produced as the organic fraction of the fuel contributes to the combustion process and inorganic components are incorporated into the cement product.
Bag filters harvest dust and put it back into the system while gases are also cleaned in the process, resulting in mainly water vapour leaving the chimney stack. This, he says, is “a different [MANUFACTURING]process to what people perceive”.
Cement kilns versus incinerators
There are key differences between a cement kiln and an incinerator. Operating temperature is significantly higher inside a kiln. A closed process and higher temperatures mean no ash is produced unlike an incinerator. Critically, cement industry achieves much higher efficiency rates, which “demonstrates what the cement can bring to the party”.
Fuels and raw materials are tested to ensure they meet the agreed specifications with the help of robotics, in contrast to a broad range of mixed waste fed into incinerators. Using sophisticated software in the control room, there is constant evaluation of inputs. Some 17,000 bits of data per second are processed, allowing real-time adjustment. Unlike the waste industry, there is certification at every stage. It’s a factory making a product, Gilmore says; “the second most used material on the planet” after water.
Platin has become one of the most modern and energy-efficient cement factories in Europe but needs to go further on fuel use, he adds. The original fossil fuel used in its kilns was heavy fuel oil. It was replaced by coal, and then by petroleum coke in the 1980s. SRF has been used since 2011 as a partial fuel replacement.
Air quality
On air quality, he cites the latest EPA’s air quality report (for 2016) which identifies the primary source of particulate matter (PM2.5) pollution in Ireland as “the continued use of solid fuel burning for home heating”, while traffic is the greatest generator of NO2 particularly in urban areas
Emissions from large industrial facilities “are well regulated under its licensing regime and further downward pressure will be realised” by the EU industrial emissions directive, it concluded.
Concentrations of dioxins/furans and PCB pollutants, which can arise from combustion or incineration processes, “remain at a consistently low level in the Irish environment”, it found. There has been no increase above background levels since the introduction of SRF, proving the process “is inherently safe”, he says.
Limerick front
The upholding of planning permission from Limerick City and County Council provides for the use up to 90,000 tonnes of alternative fuels in a €10 million project at Mungret. Much of a four-day planning hearing in Limerick concentrated on the proposal to include waste tyres as fuel - it's a well-established fuel; in Germany 200,000 tonnes of waste tyres are used annually in such circumstances.
The main objectors Limerick Against Pollution has decided not to pursue a judicial appeal of the outcome but to concentrate efforts on objecting to a new EPA licence.
In advance of a protest march in Limerick last May, which was supported by many city councillors and TDs, Gilmore said Irish Cement recognised people may have concerns about their plans in Mungret, and acknowledged individuals had the right to express their opinion. He stressed, however, the need for factual information “to allow for more informed discussion and debate”.
He cited the Bord Pleanála finding that the project “would not be prejudicial to public health, would be acceptable in terms of traffic safety and convenience and would be in accordance with the proper planning and sustainable development of the area”.
He admits, none the less, it’s a very complex area and open to misinterpretation, and there is an obligation on Irish Cement to communicate how the process works.
“We have made great progress in Platin since 2011 when we first introduced alternative fuels to replace fossil fuels in our cement kiln. Last year we avoided the importation of over 53,000 tonnes of fossil fuels and reduced our carbon dioxide emissions by over 64,000 tonnes. This permission will allow us to recover more valuable resources, make the factory more competitive and support existing and future employment.”
Clearing planning and EPA hurdles will secure the future of the plant and its 140 full-time employees, who play a critical role in ensuring Ireland has an indigenous cement industry, he says. Platin has the added advantage of being near the Dublin region where most of its customers are based.
Gilmore is reassured there is big demand for cement and concrete, especially as housing is scaled-up in coming years. “Based on the ongoing recovery in the construction sector here in Ireland, we expect the demand for cement to continue to grow with an associated increase in the need for fuel.”