Vincent Cleary, the managing director of Glenisk yoghurt factory, in Killeigh, Co Offaly, steps out of his car in the plant's yard to say hello. The car has become his on-site office since last month's devastating fire.
Five miles away, in Tullamore, some staff are working out of rooms in the Tullamore Court Hotel, while another team operates from the former Tullamore Dew premises, as everyone tries to get back into operation before Christmas.
Cleary has been humbled frequently during recent weeks by the kindness of friends, neighbours, strangers, including Taoiseach Micheál Martin, whose calls he missed.
Offers of help came in from every co-op, every dairy, not only in Ireland, but on these islands and further afield
The examples are many. A colleague spoke with the Tullamore Court Hotel about room rates to house office staff: “She came back and said they won’t take our money. It’s embarrassing at this stage how good everyone has been to us.”
But a longer-term solution was required, so he approached local business man Seamus O’Kane, who owns the vacant Tullamore Dew building. “He handed me the keys and said no rent for a year, I said, ‘Please take my money’ and he said, ‘No, I won’t take your money’.”
Offers of help came in from "every co-op, every dairy, not only in Ireland, but on these islands and further afield," he says, adding that Glenisk hopes to have "some semblance of manufacturing" back by Christmas at the adjoining Tullamore Dairies plant.
“We’re coming full circle.”
In the early 1980s Vincent's father, Jack Cleary, established Tullamore Dairies on his farm. Almost 40 years later, six members of the Cleary family still work for the company, which expanded in the 1990s to include the Glenisk brand.
“There are 14 of us. My father’s motivation was to provide employment for his family, we were his workforce. He quite rightly pointed out to us that we didn’t have too many options,” he told The Irish Times. Today, the workforce even includes cousins.
In fairness to them, I expect [our competitors are] very busy at the moment, now that we're off the shelves
The original Tullamore Dairies plant was fortunately upwind of last month’s catastrophic fire and once power was restored, goat’s and cow’s milk production has recommenced. “We’ve rented a generator, a boiler, whatever we could rent to get back up and operational within a few days.”
Ironically, builders were already on site working on a new warehouse. Now, manufacturing is going to move into that building, while the burned buildings at the front will be demolished. Cleary hopes for a speedy planning decision.
Before the fire, Glenisk had 105 different products – low fat and high protein yoghurts, different sizes of pots, including ones for the catering trade, and others. Today, the plan is to begin with 10 and slowly scale up.
The departure of Glenisk from the shelves has left gaps for other yoghurt companies, who Cleary describes as friends rather than competitors: “In fairness to them, I expect they’re very busy at the moment, now that we’re off the shelves,” he says.
Cleary describes [the fire] as a 'setback', but one that creates an opportunity to introduce the latest technologies with the lowest environmental impact
Meanwhile, all 90 Glenisk staff are still on the payroll, though they are doing different jobs. Everyone has a role to play in getting operations back, even if that means wielding a paint brush or emptying the burned premises.
“We’ll keep it going as long as we possibly can until we’re back in production and then we’ll hopefully be running shifts to bring in as many personnel as we can as we’ll have a limited amount of production.”
More than half have been with the firm for more than 20 years, he says. “I’d like to think we have a low turnover of staff because we respect them, we have almost a waiting list of people hoping to join our company. I like to think we look after our people – as we’re trying to do at the moment.”
While some might consider the fire a fatal blow, Cleary describes it as a “setback”, but one that creates an opportunity to introduce the latest technologies with the lowest environmental impact: “We’ll be a better company after than we were before,” he says.
Ironically, Glenisk had installed four electric charging points this year, powered by roof solar panels, so that staff could avail of free electricity: “That was to give them an extra reason to love Glenisk,” he says.
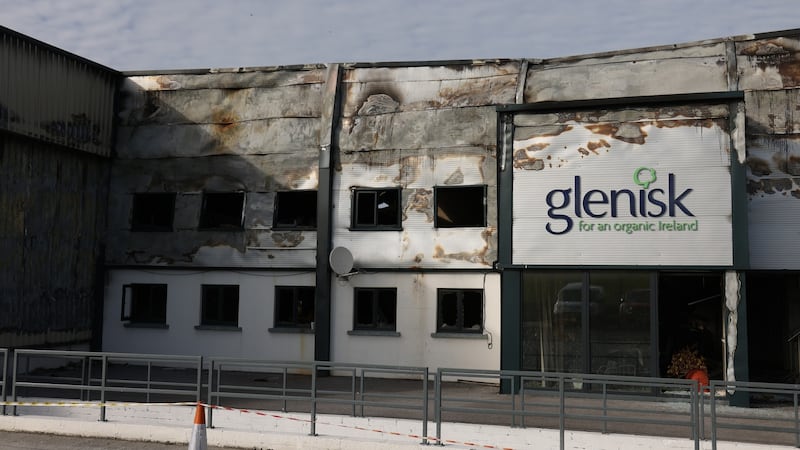
While the fire might have been bad luck for Glenisk, he says, he was determined it would have some benefit for Self Help Africa, the aid organisation with which the Offaly yoghurt brand has a long association.
“We asked customers if they couldn’t buy Glenisk to make a donation to Self Help Africa and to buy another Irish yoghurt instead. It might have been bad luck for us, but it should be an opportunity for other Irish yoghurt manufacturers.”
The aid organisation reported an "explosion" of donations – 1,000 in 48 hours – following the appeal. "At first we didn't know what had happened," says Self Help Africa's director of business development Martha Hourican. "Then we saw [the Glenisk] tweet."
Back at his car, Cleary is still going through hundreds of messages on his phone. “The Taoiseach left me two voicemail messages, which embarrassingly I only picked up at the weekend, almost two weeks after the event.”
"The head of Enterprise Ireland, Leo Clancy, the head of Bord Bia, Tara McCarthy – almost every CEO in the dairy industry, every private yoghurt manufacturer and all of our retail customers, the people who buy our products every week – they've all been leaving messages, they filled my voicemail box.
“People have sent Mass cards, novenas were said for us, some even sent financial contributions, which we have forwarded to Self Help Africa,” says Cleary.
Meanwhile, work continues. He is not looking forward to seeing the damaged building being torn down, but it will offer some sense of closure. “The sooner we can get this site cleared and start working on a replacement factory [the better].
“I’m trying to keep the emotion to one side or in check. We love this building, there’s 30-plus years of blood, sweat and tears gone into it, but it’s gone,” he says. “We have to get it replaced as quickly as possible so that we’ll have it in the rear-view mirror.”