The building and construction sector is an obvious target for a “green-up”, given that it is the largest single emitter of greenhouse gases, responsible for an estimated 37 per cent of global emissions. The good news is that the industry is now focused on using smart building technology and employing sustainable practices, methods and materials to ensure that new builds and retrofits are as environmentally friendly as possible across their entire lifespan.
Ian Scouler is managing director of The Materials Solutions Group (tMSG). He says that in every construction project today sustainability is an integral part of the conversation: “I think the bigger picture of planning development probably still needs progressive thinking but there is no doubt that we are moving in a positive direction, with sustainability being to the fore.”
Innovative, alternative solutions are increasingly hitting the marketplace, says Scouler, driven by consumer preferences, Government incentives such as grants, and increased regulation. “Every sector that we operate in today is demanding more sustainable solutions,” Scouler notes.
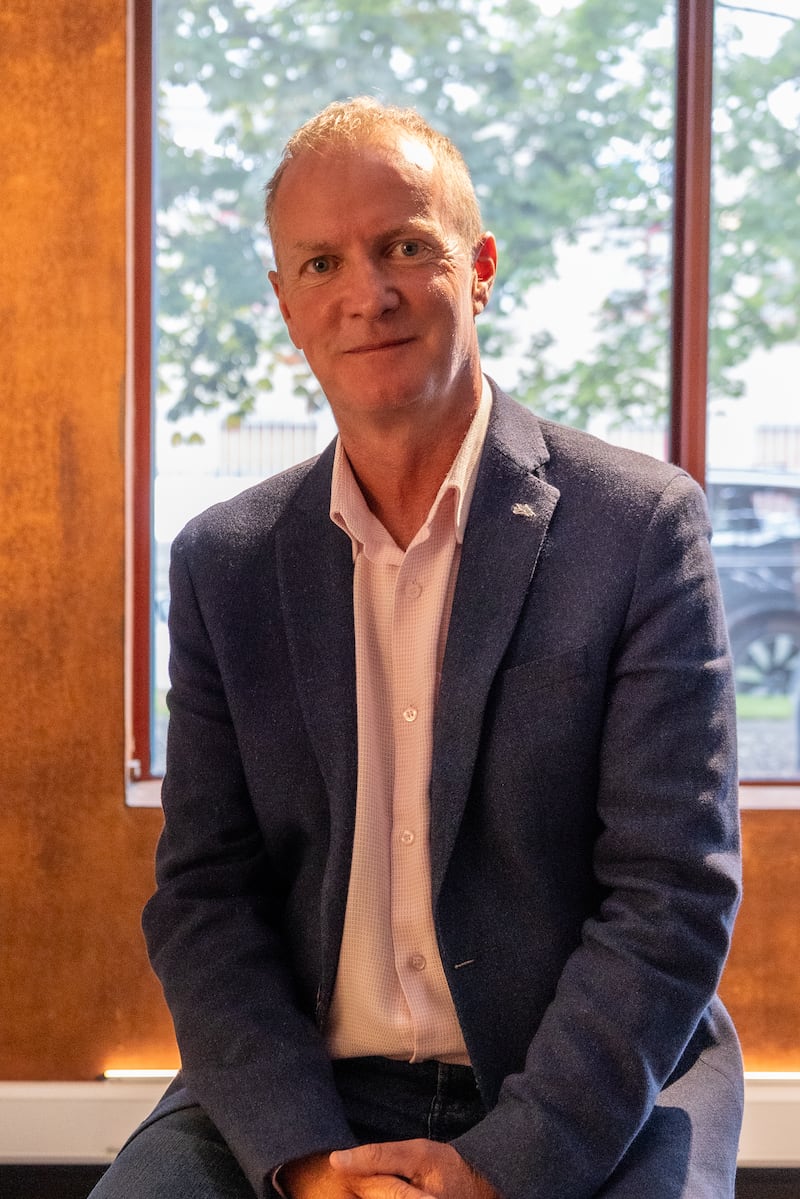
“Sustainability within the construction sector is almost predictable nowadays as everyone talks about bringing green buildings to the market by refurbishing and retrofitting,” says Jonathan Smartt, co-founder and director of Think PM. “Things like eco concrete make the headlines but people forget about the fit-out and the finer details involved in that.”
It is within this space that some of the most impressive innovations are being seen. For example, Think PM offers acoustic soundproofing solutions, which are now being fabricated with felt made from 70 per cent recycled drinks bottles. While much of this is manufactured in China and Australia, Smartt notes that the company is managing to source more from Irish and European suppliers as they attempt to green their entire supply chain.
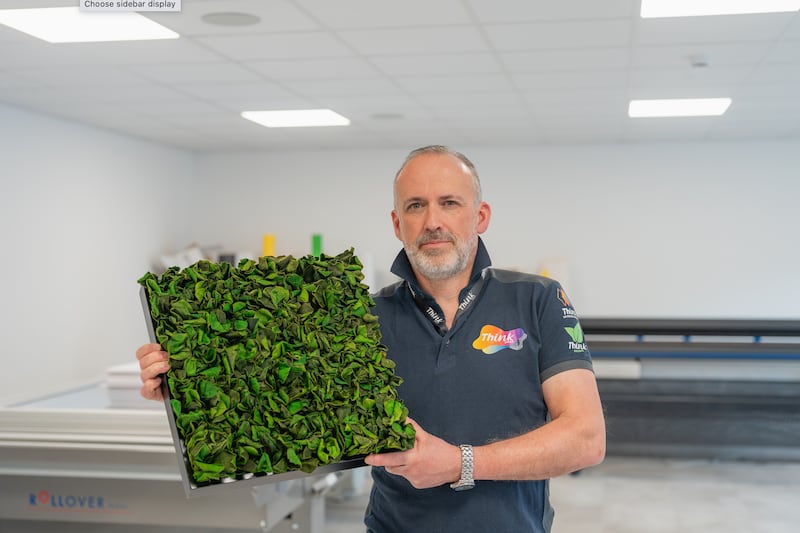
Technology is driving this revolution, says Scouler. “For example, we use honeycomb cardboard sheets that are integrated into the workflow of a precast concrete manufacture,” he says. “This is replacing wood and steel for mould production, meaning a significantly lower carbon footprint. The software and cutting-edge machinery make all this possible.”
Other innovations include “smart gloss” solutions where a film is retrofitted to glass windows; Scouler explains these architectural window films can be controlled remotely to prevent glare, bringing thermal benefit as there is reduced heat loss.
“We also offer low-flow-temperature underfloor heating systems that can be controlled via an app and involve much lower running costs compared to radiators,” he says. “They also have a much lower carbon footprint compared to embedding a water pipe in a cement screed, which takes much longer to heat up.”
Facade wrap vinyl also offers a sustainable alternative for upgrading external building cladding panels.
“Such panels are very often produced today with a powder-coated paint finish,” says Scouler. “Powder coating contains hazardous chemicals and its lifespan before refurbishment requirement is around one to two years, like any house needing repainting. Facade wrap has no hazardous chemicals and has a lifespan warranty to hold its colour for 12 years.”
Eoghan Considine is specification manager with Pipelife, which supplies pipes and fittings for the plumbing, construction and agricultural sectors. “While we definitely have a long way to go in the construction industry there have been huge strides made over the last few years on improving our sustainability credentials,” he says. “Sustainability is baked into designs from inception now, which is great to see.”

Sustainable options are now a must have, not a nice to have, Considine says. “As Ireland’s largest plastic pipe manufacturer, we focus not only on providing products that provide sustainable solutions for waste and water, we also ensure the products we manufacture are as sustainable as they can be by using sustainable materials and work practices,” he adds. “We also have Pipelife Eco within our company which focuses on renewable heating systems such as heat pumps, underfloor heating and mechanical ventilation systems to ensure new homes and renovations can meet their sustainability goals.”
Any business within the construction sector that is serious about sustainability must have that ethos embedded throughout its whole operation, says Considine, from the materials it uses and the energy it consumes to its day-to-day work practices. Where possible Pipelife uses recycled materials in its product range, he adds.
“We are also in the process of developing life-cycle analysis and environmental product declarations for a number of our products so that we can quantify the environmental impact and embodied carbon within these products,” says Considine. “Pipelife is also upskilling a number of staff in sustainability leadership to guarantee that sustainability is a core focus throughout all departments in the business.”
Sustainability in construction is becoming a key focus, agrees Darragh Ryan, head of commercial with Etex Group which includes Remagin off-site steel framing solutions.
“The drive for sustainability in construction is accelerating, with a strong emphasis on reducing carbon emissions, improving efficiency and minimising waste,” he says.
One of the most effective solutions is 2D light gauge steel (LGS) construction. “LGS structures are significantly lighter than traditional concrete or timber, reducing foundation requirements,” Ryan explains.
Precision manufacturing in a controlled environment cuts material waste by up to 90 per cent, while the 100 per cent recyclability of LGS further enhances its environmental credentials. Prefabricated panels enable construction times to be reduced by up to 30 per cent, with factory production also mitigating weather-related delays.
The energy efficiency of LGS buildings is another key advantage, says Ryan. “As developers seek to balance sustainability with cost and efficiency, LGS presents a significant advantage to traditional methods and the Remagin system offers a genuine step towards high-performance, sustainable construction. We are moving beyond rhetoric to deliver real environmental impact.”
Yet cost remains a barrier to widespread adoption, he warns: “Many projects are unable to absorb the price premium associated with sustainable solutions, leading to slow adoption unless financial incentives – such as tax breaks or long-term savings – are in place. Until sustainability is more financially viable, and greenwashing is addressed, many so-called ‘eco-friendly’ initiatives risk being more about image than real environmental benefit.”